Variable overhead efficiency variance
However, overheads are still vital to business operations as they provide critical support for the business to carry out profit making activities. For example, overhead costs such as the rent for a factory allows workers to manufacture products which can then be sold for a profit. Overheads are also very important cost element along with direct materials and direct labor. The efficiency variance is the difference between the actual unit usage of something and the expected amount of it. The expected amount is usually the standard quantity of direct materials, direct labor, machine usage time, and so forth that is assigned to a product.
How is absorption costing treated under GAAP?
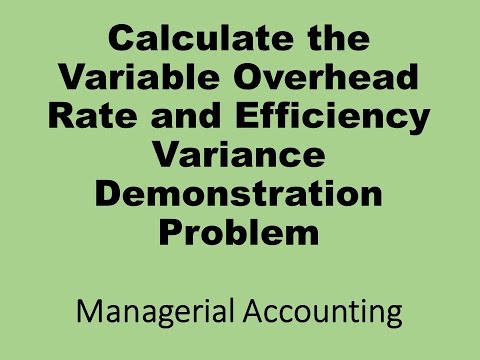
If Connie’s Candy produced 2,200 units, they should expect total overhead to be10,400 and a standard overhead rate of4.73 (rounded). In addition to the total standard overhead rate, Connie’s Candy will want to know the variable overhead rates at each activity level.
This compares the actual variable overhead for production achieved with the budgeted. It is calculated by deducting the actual variable overhead incurred from a product of standard variable overhead rate and actual hours incurred. It measures the difference between the budgeted and the actual level of activity valued at the standard fixed cost per unit. The fixed overhead volume variance is obtained by subtracting actual units produced from budgeted units and then multiplying the result with standard fixed cost per unit. The standard fixed cost per unit is obtained by dividing the budgeted fixed overhead by the budgeted production.
It can also be obtained by subtracting actual hours incurred in production from the budgeted hours and then multiplying the result with the standard fixed cost per hour. It is favorable when the actual units produced are more than the budgeted units and adverse when the number of units produced are less than the budgeted. Fixed overhead variance analysis uses your standard costs or quantities produced as the benchmark. The actual overhead cost or quantity produced is calculated and compared against the benchmark. By analyzing the standard overhead and actual overhead, you can determine if you are running over or under budget.
This is the difference between the actual and budgeted hours worked, which are then applied to the standard variable overhead rate per hour. Variable overhead tends to be small in relation to the amount of fixed overhead. Since it varies with production volume, an argument exists that variable overhead should be treated as a direct cost and included in the bill of materials for products.
What is the variable overhead rate variance and the variable overhead efficiency variance?
In numerical terms, variable overhead efficiency variance is defined as (actual labor hours less budgeted labor hours) x hourly rate for standard variable overhead, which includes such indirect labor costs as shop foreman and security.
For example, say a company budgeted for 20 labor hours but only used 16 and the standard overhead rate is $5 per hour. A favorable overhead variance, like this one, means that less overhead costs were spent to create the product than expected. If the variance is negative, that means that more hours were spent on the product than expected, and more overhead costs were incurred.
For example, assume your small business budgets 410 labor hours for a month and that your employees work 400 actual labor hours. Your labor efficiency variance would be 410 minus 400, times $20, which equals a favorable $200.
Wages paid to supervisors, janitorial staff, machine parts and machine maintenance are all common overhead costs. A business usually applies these overhead costs based on the number of labor hours incurred to create products.
Variable costs include direct labor, direct materials, and variable overhead. Labor price variance, or rate variance, measures the difference between the budgeted hourly rate and the actual rate you pay direct labor workers who directly manufacture your products. Labor efficiency variance measures the difference between the number of direct labor hours you budgeted and the actual hours your employees work. Compare these two variances to determine how well your small business managed its direct labor costs during a period. To calculate overhead efficiency variance, subtract the budgeted labor hours from the actual hours expended and multiply by the standard overhead rate per hour.
Fixed overhead refers to your indirect manufacturing costs that do not vary with production, such as your building or factory rent, utilities, property taxes, depreciation and insurance expenses. For example, the number of labor hours taken to manufacture a certain amount of product may differ significantly from the standard or budgeted number of hours. Variable overhead efficiency variance is one of the two components of total variable overhead variance, the other being variable overhead spending variance.
What Is Variable Overhead Efficiency Variance
Direct labor hours are the hours spent by the individuals that actually create or modify the product. To calculate direct labor efficiency variance, subtract the budgeted labor hours from the actual hours expended and multiply by the budgeted cost of labor per hour. For example, if a company thought it would need 20 labor hours at $30 per hour for a product but only needed 16 hours, the variance is 4 multiplied by $30, or $120.
How do you calculate variable overhead efficiency variance?
The variable overhead efficiency variance is the difference between the actual and budgeted hours worked, which are then applied to the standard variable overhead rate per hour. The formula is: Standard overhead rate x (Actual hours – Standard hours)
- A business measures its manufacturing and selling efficiency by examining any volume variances it incurs during production and sales.
The fixed overhead efficiency variance measures how efficient your employees are at manufacturing your products. The fixed overhead efficiency standard is your expected labor costs for producing a set number of units. To find the variance amount, subtract the actual hours from the standard hours and multiply that figure by the standard labor rate. For example, subtract four standard hours from the actual five hours to get a one hour unfavorable variance.
Variable Overhead Efficiency Variance
Yield variance is the difference between actual output and standard output of a production or manufacturing process, based on standard inputs of materials and labor. Variable cost changes with the level of output, as such is increased when a higher number of units are produced. Direct material cost, direct labor, and variable overheads are main types of variable costs. Thus, if the increase in output is avoided, the related costs can be controlled. Although increasing production usually increases the total cost of variable overhead, efficiencies can occur as more products are produced.
Variable costs are in contrast to fixed costs, which remain relatively constant regardless of the company’s level of production or business activity. Combined, a company’s fixed costs and variable costs comprise the total cost of production.
Multiply the one hour unfavorable variance by the $8 standard rate and you have an unfavorable labor variance of $8 per unit. In business, overhead or overhead expense refers to an ongoing expense of operating a business.
A business measures its manufacturing and selling efficiency by examining any volume variances it incurs during production and sales. A volume variance is the difference between what a company expected to use and what it actually used. Volume variance can be applied to units of sales, direct materials, direct labor hours and manufacturing overhead. The basic formula for volume variance is the budgeted amount less the actual amount used multiplied by the budgeted price.
For example, an efficiency variance can be calculated for the number of hours required to complete an audit versus the budgeted amount. Often, explanation of this variance will need clarification from the production supervisor. Another variable overhead variance to consider is the variable overhead efficiency variance. Direct labor volume variance – also called direct labor efficiency variance — is the difference between the amount of direct labor hours budgeted and the actual hours expended.
In accounting, all costs can be described as either fixed costs or variable costs. Variable costs are inventoriable costs – they are allocated to units of production and recorded in inventory accounts, such as cost of goods sold. Fixed costs, on the other hand, are all costs that are not inventoriable costs. All costs that do not fluctuate directly with production volume are fixed costs. Fixed costs include various indirect costs and fixed manufacturing overhead costs.
Overheads are the expenditure which cannot be conveniently traced to or identified with any particular cost unit, unlike operating expenses such as raw material and labor. Therefore, overheads cannot be immediately associated with the products or services being offered, thus do not directly generate profits.
This rate is determined in advance then applied when actual labor hours are calculated. The standard overhead rate is the total budgeted overhead of10,000 divided by the level of activity (direct labor hours) of 2,000 hours. Notice that fixed overhead remains constant at each of the production levels, but variable overhead changes based on unit output. If Connie’s Candy only produced at 90% capacity, for example, they should expect total overhead to be9,600 and a standard overhead rate of5.33 (rounded).
In accounting, variable costs are costs that vary with production volume or business activity. Variable costs go up when a production company increases output and decrease when the company slows production.
Also, price discounts on larger orders of raw materials—due to the ramp-up in production—can lower the direct cost per unit. Additional factors that may be included in variable overhead expenses are materials, changes in the labor force, and maintenance of equipment. Labor efficiency variance equals the number of direct labor hours you budget for a period minus the actual hours your employees worked, times the standard hourly labor rate.
It is entirely possible that an improperly-set standard number of labor hours can result in a variance that does not represent the actual performance of an entity. Consequently, investigation of the variable overhead efficiency variance should encompass a review of the validity of the underlying standard.
This is the difference between the actual and budgeted variable overhead costs that result from inefficient use of indirect materials and indirect labor. Variable overhead efficiency variance is calculated by subtracting the standard budgeted hours from the actual hours incurred, and then multiplying the result with the standard variable overhead rate. A favorable variance results when the actual hours used are less than the budgeted while an adverse variance results from use of more hours than the budgeted. Overhead volume variance, also called overhead efficiency variance, is the difference between the amount of overhead applied and the actual overhead applied. Overhead is all the product costs that a company incurs that aren’t part of direct labor or overhead.