Reorder points: Reorder Point Formula: How Your Business Can Use It
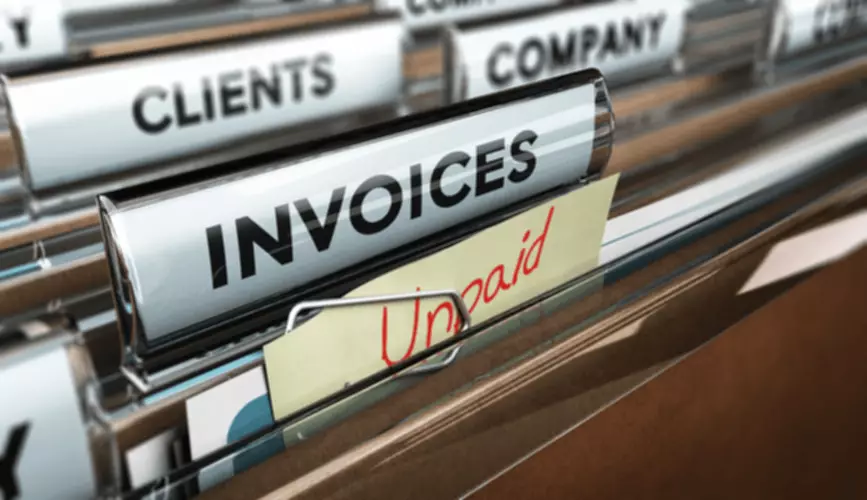
If the delivery of an item is delayed or the consumption rate increases rapidly and unpredictably for any reason, the safety stock will cover the shortage of items. Reorder points can be calculated and maintained using pen and paper or spreadsheets programs like Excel. However, modern inventory management systems usually have various degrees of ROP functionality built-in that automatically trigger parts of the stock replenishment process. Modern solutions often use ROPs in conjunction with constraints management and other advanced forecasting methods, enabling deeper insights into stock consumption. This formula takes into account costs related to set up, production, and storage, as well as other factors that include demand. The aim is to specify the most favorable product quantity for your business that goes beyond your replenishment schedule.
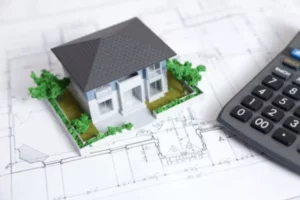
Safety stock is similar to a reorder point, but it’s a surplus quantity to ensure you don’t run completely out of stock if there are delays. NetSuite has packaged the experience gained from tens of thousands of worldwide deployments over two decades into a set of leading practices that pave a clear path to success and are proven to deliver rapid business value. With NetSuite, you go live in a predictable timeframe — smart, stepped implementations begin with sales and span the entire customer lifecycle, so there’s continuity from sales to services to support. The reorder point formula shows what happens in an ideal scenario, but things may work out differently in practice than they do in theory. Now we’ll plug the figures from our example into the reorder point formula. Either you have to carry that inventory, let’s say from today to tomorrow, or let’s say from this week to next week, or this month to next month – and inventory holding is always costly.
The reorder point formula video
If it’s a sought-after item, these delays can often come at the worst possible time. The daily sales velocity, or the average number of units you sell per day, differs for everything you sell. Understanding how to manage your stock levels, calculate reorder points, and when to replenish your inventory ensures your business maintains a competitive edge. So now you know the reorder point formula, but what about demand during lead time? In this section we break down ROP and tell you exactly how to calculate it. ROP stands for reorder point, which tells a business when to place an order (where the “when” is given in terms of current inventory levels).
- When you place the order also affects the lead time (compare orders during a busy and slow season).
- It usually triggers the purchase of a predetermined amount of replenishment inventory.
- For figuring out an optimal amount of units – and to help improve operations and reduce costs – figure out your economic order quantity.
- Our partners cannot pay us to guarantee favorable reviews of their products or services.
- Look beyond supply and demand and develop comprehensive material requirements planning, which involves optimizing many critical components, including purchase order, forecasting, marketplace demand, and data management.
- To accurately calculate a product’s reorder point, it’s important to understand these factors and how they might impact your sales velocity.
This formula alteration means that replenishment stock will be ordered sooner, which greatly reduces the risk that there will be a stockout condition. However, it also means that a company will have a larger investment in its on-hand inventory, so there is a trade-off between always having available inventory and funding a larger inventory asset. Look beyond supply and demand and develop comprehensive material requirements planning, which involves optimizing many critical components, including purchase order, forecasting, marketplace demand, and data management. To capture safety stock, you can input “buffer days,” which are additional days factored in with a vendor’s lead time to increase the number of units ordered. Once you have your safety stock number, you can then plug it into the reorder point formula for insight in your reorder levels.
How to calculate and set reorder points
A reorder point, or ROP indicates an inventory item’s minimum stock level at which new stock should be ordered in order to avoid a stockout. In other words, the reorder point is the lowest number of units of an SKU that a company needs to have in stock to make sure it can keep fulfilling orders. It can thus also be viewed as the last time to replenish stock to avoid a stockout.
You’ll have enough shirts left on hand units – to sustain you until the next delivery of shirts. It also saves you money long-term by trimming inventory with lower sales. However, many retail companies don’t give their stock orders the attention needed to manage them correctly. Get pricing below and learn more about why thousands of brands work with ShipBob’s ecommerce fulfillment services.
Safety stock
InFlow Cloud has a Recommended Reorder Point report that examines your sales data and recommends reorder points for your products. It also factors in goods in transit (GIT), which are products that have been ordered from a vendor but haven’t been received yet. Unlike spreadsheets, inFlow was designed specifically for working with inventory. A reorder point is a fairly straightforward concept, but successful implementation requires paying attention to nuance and details about the business, suppliers and customers.
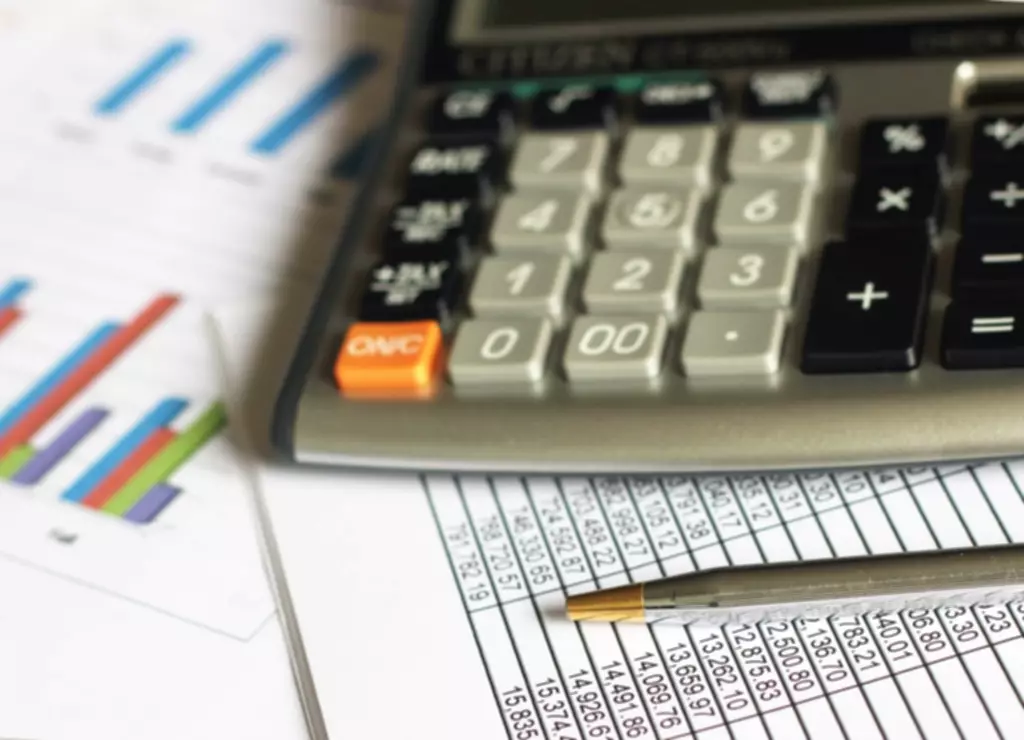
Recalculate your ROP whenever you experience major changes to maintain optimal stock levels. The reorder point for replenishment of stock occurs when the level of inventory drops down to zero. In view of instantaneous replenishment of stock the level of inventory jumps to the original level from zero level. Regular audits spot trouble sooner and identify opportunities for improvements.
Sales or manufacturing rate
In this theoretical world, you’d be running a business with no need for inventory, placing orders as the customers come to you and having your customers served instantly. The purpose of a reorder point is to find and set the lowest stock level for an inventory item at which a new order should be put in, in order to avoid a stockout. Your reorder point is a critical factor, along with safety stock, in the larger scheme of inventory management and your supply chain. Your suppliers encounter trouble fulfilling an order – via shipping, manufacturing, or a shortage of raw materials. The safety stock ensures you can still fulfill orders if these happen while you wait for new inventory to arrive. Delays with your suppliers create headaches with your inventory management, resulting in a scarcity of your product.
Avoid stockouts
For example, ABC International uses an average of 25 units of its green widget every day, and the number of days it takes for the supplier to replenish inventory is four days. Therefore, ABC should set the reorder point for the green widget at 100 units. When the inventory balance declines to 100 units, ABC places an order, and the new units should arrive four days later, just as the last of the on-hand widgets are being used up. Modern manufacturing ERP systems utilizing forecast-based MRP methodology are generally much easier to use, and more reliable than setting up effective ROPs for your whole manufacturing or distribution enterprise. MRPeasy not only automates and simplifies stock replenishment, but also tracks and manages many other aspects of inventory, helps in scheduling and planning production, includes integrated cost accounting, and much more. The reorder point (ROP) is the minimum inventory or stock level for a specific product that triggers the reordering of more inventory when reached.
Demand during lead time
Even simple calculations can yield valuable guidelines, and further customization can turn a challenging part of inventory management into an almost automatic process that rarely demands much worry or intervention. Investments in setting up smart reorder points today can yield dividends in efficiency for years to come. There’s a simple formula that businesses can use to determine the reorder point for a product, taking into account customer demand and vendor delivery times.