Material variance
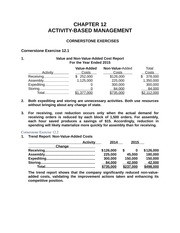
If there wasn’t enough supply available of the necessary raw materials, the company purchasing agent may have been forced to buy a more expensive alternative. If the company bought a smaller quantity of raw materials, they may not have qualified for favorable bulk pricing rates. Because the company uses 30,000 pounds of paper rather than the 28,000-pound standard, it loses an additional $20,700.
How to Calculate Material Price Variance
To compute the direct materials price variance, subtract the actual cost of direct materials ($297,000) from the actual quantity of direct materials at standard price ($310,500). This difference comes to a $13,500 favorable variance, meaning that the company saves $13,500 by buying direct materials for $9.90 rather than the original standard price of $10.35.
As standard costs, those are the estimates of what you expect to spend. $10 times 1000 units creates a $10,000 unfavorable variance for labor, since it costs you more money. Meanwhile, let’s say that you got your raw materials at $180 per unit.
Direct material variance
The first step in activity-based variance analysis is to assign all overhead costs to a level of activity. To reach this standard rate, the annual overhead cost is divided by the cost center’s practical capacity. Practical capacity is used so that idle capacity may be found and put to better use.
Lumber costs may rise due to increased fuel costs and then lower when diesel prices stabilize. In food service, the price of ingredients, such as milk and eggs, is always changing. When your business purchases others goods to produce your products, you must incorporate the cost of the supplies into your budgets at the beginning of the year and each month.
The inventory business unit’s currency in this example is U.S. dollars (USD). There is always the chance that a supplier may change the final price after a standard cost has been set. Variances allow for accountants to still refer to a standard cost, but point out exactly how much the final cost differs from the standard cost. Standard direct labor costs are the costs associated with producing a product.
This is the difference between the standard and actual cost per unit of the direct materials purchased, multiplied by the standard number of units expected to be used in the production process. Direct materials are a part of your company’s inventory along with your direct labor costs and any manufacturing overhead costs associated with making your products. Calculating direct materials cost requires knowing how much your company has actually spent on the materials used during production over the period. Having this information allows you to analyze your inventory costs and determine your work-in-progress inventory, which is inventory that is not completely finished at the time you do your analysis.
Purchase price variance
We compared standard cost to the ability of a household to budget food costs for a month. Through this, we saw how it acts both as a guideline for appropriate spending habits for those who may not purchase routinely, as well as a better way to plan for future spending. To find the standard cost, we add the standard labor cost, the standard materials cost, and the standard overhead cost. Variances from this could be favorable if they resulted in a cheaper final product or unfavorable if they cost the company more.
Direct materials for the period is $3,000 plus $10,000 less $2,000, or $11,000. The difference between the standard cost of direct materials and the actual cost of direct materials that an organization uses for production is known as Material Variance. So let’s say that you were producing a good and had set standard costs for labor at $100 per good and the standard cost for materials at $200 per unit.
- If the voucher is not available when you run the Transaction Costing process, then the system calculates the difference between the standard cost and the PO price.
- The purchase price variance is the difference between the standard costs for the material and landed cost elements and the corresponding actual costs from the matched, posted, and extracted vouchers.
What is a purchase price variance?
The purchase price variance is the difference between the actual price paid to buy an item and its standard price, multiplied by the actual number of units purchased. The formula is: (Actual price – Standard price) x Actual quantity = Purchase price variance.
Material Cost Variance gives an idea of how much more or less cost has been incurred when compared with the standard cost. Thus, Variance Analysis is an important tool to keep a tab on the deviations from the standard set by a company. The cost of raw materials changes all the time in the business world.
For purposes of inventory calculation, the direct materials account includes the cost of materials used rather than materials purchased. To calculate direct materials, add beginning direct materials to direct materials purchases and subtract ending direct materials. For example, say that a company had $3,000 worth of flour stock at the beginning of the year, bought $10,000 worth of flour during the year, and has $2,000 worth of flour remaining at year end.
If you’re looking for the PPV per unit, divide the total PPV by the number of units purchased by your business. To determine the total PPV for a specific order, subtract the standard amount from the actual amount. If feasible, at the end of every reporting period an analysis of purchase and production costs for capitalizability should be performed.
The purchase price variance is the difference between the standard costs for the material and landed cost elements and the corresponding actual costs from the matched, posted, and extracted vouchers. Based on the timing of the voucher processing and the Landed Cost Extract process, the PPV could be computed and posted in one or two parts. If the voucher is not available when you run the Transaction Costing process, then the system calculates the difference between the standard cost and the PO price. The difference between the standard cost of direct materials specified for production and the actual cost of direct materials used in production is known as Direct Material Cost Variance.
It is usually better to compute the variance when materials are purchased because that is when the purchasing manager, who has responsibility for this variance, has completed his or her work. In addition, recognizing the price variance when materials are purchased allows the company to carry its raw materials in the inventory accounts at standard cost, which greatly simplifies bookkeeping. The material price variance calculation tells managers how much money was spent or saved, but it doesn’t tell them why the variance happened. One common reason for unfavorable price variances is a price change from the vendor. Companies typically try to lock in a standard price per unit for raw materials, but sometimes suppliers raise prices due to inflation, a shortage or increasing business costs.
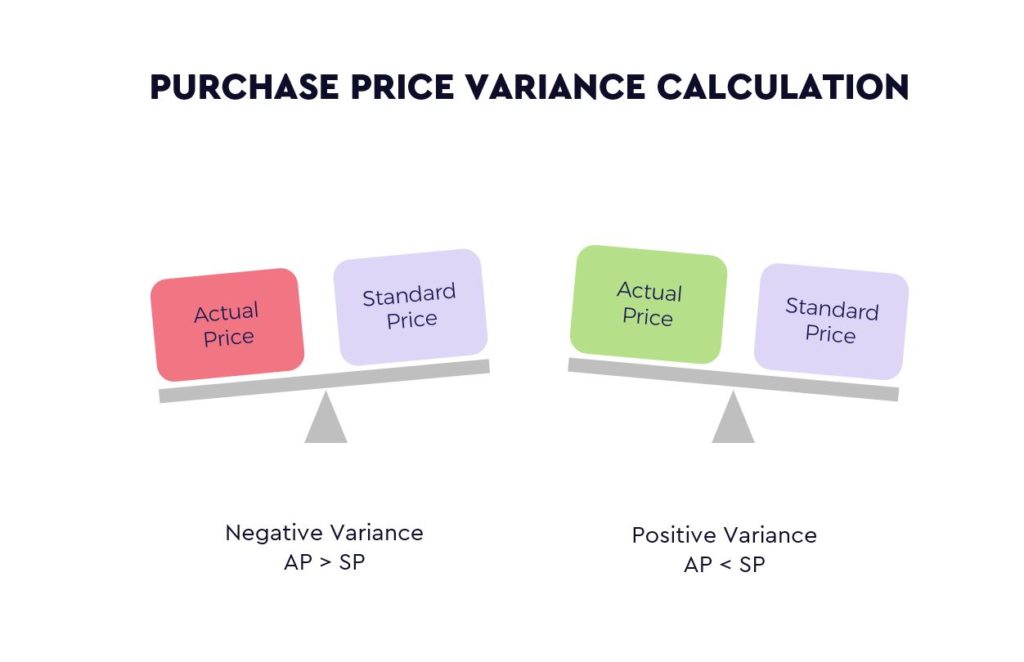
Diagramming direct materials variances
As the cost of goods changes, your amount budgeted may come in a bit high or low. For budgeting purposes, many companies determine a standard cost at the beginning of each year that is used as the estimated price of goods throughout the year. The term “purchase price variance,” or PPV variance, is used to show the difference between the estimated and actual costs in accounting.
To calculate work-in-progress inventory, add the cost of direct materials to direct labor and manufacturing overhead for the incomplete inventory. Accountants typically use standard costing to estimate the value of direct materials, direct labor and manufacturing overhead in work-in-progress inventory. Direct materials cost is the sum of all direct materials costs incurred during the accounting period.
The standard rates calculated for batch and product level activities do not vary with production volume. This is a fundamental difference between ABC and traditional variance analysis. This example illustrates the accounting entries for purchase price variance and exchange rate variance for a standard cost item.
When complete, capitalizable variances should be recorded in a “standard-to-actual” reserve within inventory on the balance sheet with the remainder being appropriately expensed through the income statement. This reserve has the effect of adjusting the company’s inventory balances to “actual,” which is appropriate under GAAP. On a net basis, the purchase price variance is really the difference between standard cost of the material and the actual invoice price of the material. The materials price variance can be computed either when materials are purchased or when they are placed into production.
The actual cost less the actual quantity at standard price equals the direct materials price variance. The difference between the actual quantity at standard price and the standard cost is the direct materials quantity variance. The total of both variances equals the total direct materials variance. In this lesson, we looked at the importance of standard costs for companies. Remember that a standard cost is the amount that you expect to pay for a good or service, especially when it comes to creating something.
How do you find the direct materials price variance?
Purchase price variance. This is the difference between the standard and actual cost per unit of the direct materials purchased, multiplied by the standard number of units expected to be used in the production process. This variance is the responsibility of the purchasing department.