Inventory Basics
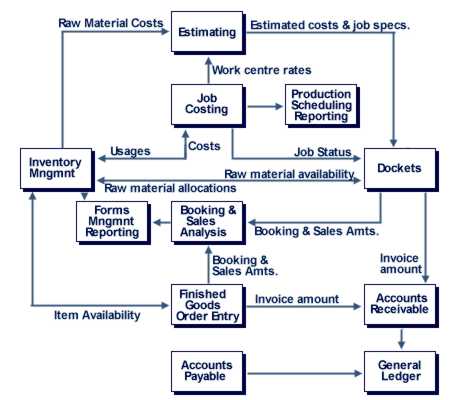
Or, if the production process is brief, bypass the work-in-process account and debit the finished goods inventory account instead. The cost of raw materials on hand as of the balance sheet date appears in the balance sheet as a current asset. Raw materials may be aggregated into a single inventory line item in the balance sheet that also includes the cost of work-in-process and finished goods inventory. Raw materials inventory is the total cost of all component parts currently in stock that have not yet been used in work-in-process or finished goods production. 1 The first step in the tire manufacturing process is the mixing of raw materials to form the rubber compound.
This gives you the ending raw materials inventory, which is the beginning inventory for the next period. Accounts payable turnover requires the value for purchases as the numerator. This is indirectly linked to the inventory account, as purchases of raw materials and work-in-progress may be made on credit – thus, the accounts payable account is impacted.
The more materials you stockpile but don’t use, the greater the risk of spoilage. You also have to pay for space to store them plus possible maintenance and transportation costs. Total beginning inventory is also important for calculating the cost of goods sold. Add together the initial value of raw materials, works in progress and finished goods to get beginning overall inventory.
For direct materials, debit the work in process inventory account and credit the raw materials inventory account. If the production process is so short that it doesn’t make sense to use a work in process account, debit the finished goods inventory instead.
How do you find raw materials inventory?
Raw materials inventory is the total cost of all component parts currently in stock that have not yet been used in work-in-process or finished goods production. There are two subcategories of raw materials, which are: Direct materials. These are materials incorporated into the final product.
In a production line, one machine/process uses the output of other machines/process. The speed of different machines may not always integrate with each other. For that reason, the stock of input for all the machines should be sufficient to keep the factory running. Based on the past experiences, a businessman is able to foresee the future trends of the market and takes certain decisions based on that.
Debit the factory overhead account and credit the raw materials inventory asset account. At the end of the month, the ending balance in the overhead account is allocated to the cost of goods sold and ending inventory. Debit the work-in-process inventory account and credit the raw materials inventory asset account.
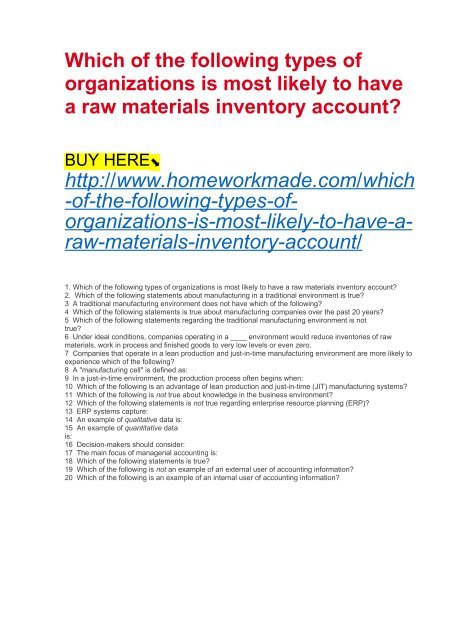
Raw materials inventory
To get the ending raw materials inventory for an accounting period, you add the beginning balance together with any raw materials purchased. Subtract the materials that were used in manufacturing, whether the goods are finished or still work in progress.
Sometimes, a firm may keep larger inventory than is necessary to meet demand and keep the factory running under current conditions of demand. These goods are maintained on hand at or near a business’s location so that the firm may meet demand and fulfill its reason for existence. If the firm is a retail establishment, a customer may look elsewhere to have his or her needs satisfied if the firm does not have the required item in stock when the customer arrives. If the firm is a manufacturer, it must maintain some inventory of raw materials and work-in-process in order to keep the factory running.
Suppose you have $5,000 of raw materials, buy $5,000 more in the period and use up $4,000. If $2,000 of the remaining materials become obsolete, your ending balance is $4,000, which will be the beginning balance of the next quarter.
Once the finished goods are sold, the cost of the raw materials should be recorded in the cost of goods sold account. Raw materials may sometimes be declared obsolete, possibly because they are no longer used in company products, or because they have degraded while in storage, and so can no longer be used. If so, they are typically charged directly to the cost of goods sold, with an offsetting credit to the raw materials inventory account.
How to Calculate Direct Materials Cost
Gigantic mixers, hanging like vertical cement mixers, stir the rubber and chemicals together in batches weighing up to 1,100 pounds. Higher sales (and thus higher cost of goods sold) leads to draining the inventory account. The conceptual explanation for this is that raw materials, work-in-progress, and finished goods (current assets) are turned into revenue. The cost of goods flows to the income statement via the Cost of Goods Sold (COGS) account.
as well as for determining the average number of days required for inventory turnover. The calculation also assumes that both ordering and holding costs remain constant. Economic order quantity (EOQ) is the ideal order quantity a company should purchase to minimize inventory costs such as holding costs, shortage costs, and order costs.
BUSINESS OPERATIONS
- Raw materials are inventory items that are used in the manufacturer’s conversion process to produce components, subassemblies, or finished products.
- They also may be objects or elements that the firm has purchased from outside the organization.
Railcars deliver large quantities of natural and synthetic rubber, carbon black, sulfur, and other chemicals and oils, all of which are stored until needed. Computer control systems contain various recipes and can automatically measure out specific batches of rubber and chemicals for mixing.
Expecting a price rise, a spurt in demand etc some businessman invests money in stocking those goods. It is normally the raw materials or finished goods and this strategy is executed by traders. Buffer inventory is the inventory kept or purchased for the purpose of meeting future uncertainties.
These are the partly processed raw materials lying on the production floor. It is unavoidable inventory which will be created in almost any manufacturing business.
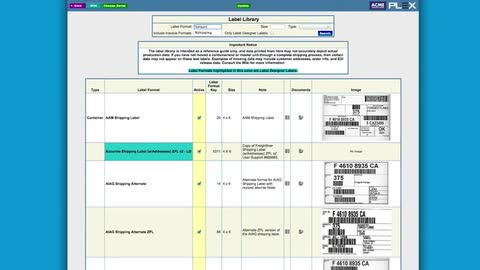
It consists of all the component parts that your company hasn’t turned into either finished goods or works in progress. Your raw materials inventory also includes indirect materials, such as lubricants or rags that you use when creating finished goods. Knowing your raw materials inventory is important for accounting and also for business efficiency.
Add raw materials purchases during the period and subtract the ending inventory balance. That gives you cost of goods sold, which helps determine your income for the period.
This production-scheduling model was developed in 1913 by Ford W. Harris and has been refined over time. The formula assumes that demand, ordering, and holding costs all remain constant. In manufacturing concern, plant and machinery should always keep running. The act of stopping machinery, costs to the entrepreneur in terms of additional set up costs, repairs, idle time depreciation, damages, trial runs etc.
You calculate and record beginning inventory so that you can calculate ending inventory. If, say, you’re making out your balance sheet, you’ll need to include inventory levels as an asset. It’s acceptable accounting practice to combine raw materials, works in progress and finished goods into a single balance sheet asset account.
Conversely, when lot sizes decrease, inventory holding/carrying costs decrease, but the cost of ordering/setup increases since more orders/setups are required to meet demand. When the two costs are equal (holding/carrying costs and ordering/setup costs) the total cost (the sum of the two costs) is minimized. Cycle inventories, sometimes called lot-size inventories, result from this process. Usually, excess material is ordered and, consequently, held in inventory in an effort to reach this minimization point. Hence, cycle inventory results from ordering in batches or lot sizes rather than ordering material strictly as needed.
In addition, it must maintain some supply of finished goods in order to meet demand. Raw materials are usually recorded on a balance sheet as an inventory asset. When recording raw materials, a debit is made to the raw materials inventory account, while a credit is made to the accounts payable account. Tracking your raw materials inventory and making a raw materials consumption analysis is also important outside of your bookkeeping.
FINANCE YOUR BUSINESS
Raw materials are inventory items that are used in the manufacturer’s conversion process to produce components, subassemblies, or finished products. These inventory items may be commodities or extracted materials that the firm or its subsidiary has produced or extracted. They also may be objects or elements that the firm has purchased from outside the organization. Even if the item is partially assembled or is considered a finished good to the supplier, the purchaser may classify it as a raw material if his or her firm had no input into its production.
For indirect materials, debit the overhead account and credit the raw materials inventory asset account. At the end of the accounting period, the balance of the overhead account is allocated to the cost of goods sold and ending inventory. If this happens, subtract them from the raw inventory account and debit cost of goods sold.
Typically, raw materials are commodities such as ore, grain, minerals, petroleum, chemicals, paper, wood, paint, steel, and food items. However, items such as nuts and bolts, ball bearings, key stock, casters, seats, wheels, and even engines may be regarded as raw materials if they are purchased from outside the firm.
Under normal conditions, a business transports raw materials, WIP, finished goods etc from one site to other for various purpose like sales, purchase, further processing etc. Due to long distances, the inventory stays on the way for days, weeks and even months depending on distances. As such, the purpose of each seems to be that of maintaining a high level of customer service or part of an attempt to minimize overall costs. When large quantities are ordered or produced, inventory holding costs are increased, but ordering/setup costs decrease.