Idle Time Variance
AccountingTools
This result means the company incurs an additional $3,600 in expense by paying its employees an average of $13 per hour rather than $12. As stated earlier, variance analysis is the control phase of budgeting. This information gives the management a way to monitor and control production costs. Next, we calculate and analyze variable manufacturing overhead cost variances.
An employer’s overhead cost per employee is also considered, in addition to the employer’s annual taxes. Each cost is added together and then divided by the employee’s hours worked per year. To compute the direct labor quantity variance, subtract the standard cost of direct labor ($48,000) from the actual hours of direct labor at standard rate ($43,200). This math results in a favorable variance of $4,800, indicating that the company saves $4,800 in expenses because its employees work 400 fewer hours than expected. To estimate how the combination of wages and hours affects total costs, compute the total direct labor variance.
The direct labor hourly rate, also known as the labor rate standard, includes the hourly pay rate, fringe benefits costs and your portion of employee payroll taxes. Calculate the hourly value of fringe benefits and employee taxes by dividing that amount by the number of hours worked in the pay period. Standard costs are used to establish the flexible budget for direct labor.
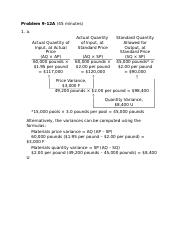
Labor Variance Defined
The flexible budget is compared to actual costs, and the difference is shown in the form of two variances. The labor rate variance focuses on the wages paid for labor and is defined as the difference between actual costs for direct labor and budgeted costs based on the standards.
Rate variance
The labor efficiency variance focuses on the quantity of labor hours used in production. It is defined as the difference between the actual number of direct labor hours worked and budgeted direct labor hours that should have been worked based on the standards.
Accounting for Managers
Companies typically try to lock in a standard price per unit for raw materials, but sometimes suppliers raise prices due to inflation, a shortage or increasing business costs. If there wasn’t enough supply available of the necessary raw materials, the company purchasing agent may have been forced to buy a more expensive alternative. If the company bought a smaller quantity of raw materials, they may not have qualified for favorable bulk pricing rates. The labor cost formula takes into account an employee’s hourly wages, the hours they work in a week, and the weeks they work in a year.
- Labor price variance, or rate variance, measures the difference between the budgeted hourly rate and the actual rate you pay direct labor workers who directly manufacture your products.
- Compare these two variances to determine how well your small business managed its direct labor costs during a period.
It is important to have a consistent employee timesheetsoftware or app for long term labor cost success. Labor price variance equals the standard hourly rate you pay direct labor employees minus the actual hourly rate you pay them, times the actual hours they work during a certain period. For example, assume your small business budgets a standard labor rate of $20 per hour and pays your employees an actual rate of $18 per hour. Your labor price variance would be $20 minus $18, times 400, which equals a favorable $800.
Fixed labor cost remains the same regardless of the company’s production output. Owners, directors, managers and supervisors are the common types of fixed labor in small business. These individuals usually earn a fixed salary regardless of the hours worked in the business. Business owners used fixed salaries to avoid paying managers and supervisors overtime during business operations.
Direct labor includes wages plus employer-paid payroll taxes like Social Security and Medicare tax. It also includes other benefits such as worker’s compensation and unemployment insurance, health insurance and contributions to pension or retirement plans.
Compare these two variances to determine how well your small business managed its direct labor costs during a period. Once the total overhead is added together, divide it by the number of employees, and add that figure to the employee’s annual labor cost. To compute the direct labor price variance, subtract the actual hours of direct labor at standard rate ($43,200) from the actual cost of direct labor ($46,800) to get a $3,600 unfavorable variance.
Direct Labor Rate Variance Calculation
As with direct materials, the price and quantity variances add up to the total direct labor variance. Suppose XYZ Widgets employs a direct labor workforce of 10 people, who work 40 hours per week, and they earn an average of $18 per hour. Total wages are equal to 40 hours multiplied by $18 and then multiplied by 10. Additional payroll taxes and benefits total $1,800, which gives a total direct labor weekly payroll expenditure of $9,000.
Ten workers normally work 400 hours in a week, so the standard or average cost of one hour of direct labor equals $9,000 divided by 400, or $22.50. Some of the workers in a factory perform tasks that are directly linked to the manufacturing process. Other factory floor employees are considered indirect labor because their jobs are not immediately tied to making the product. Equipment maintenance technicians and security guards fall into this category. The difference is crucial because only direct labor is counted as part of the cost of manufacturing a good.
What causes labor rate variance?
The labor rate variance is found by computing the difference between actual hours multiplied by the actual rate and the actual hours multiplied by the standard rate.
To calculate the labor burden, add each employee’s wages, payroll taxes, and benefits to an employer’s annual overhead costs (building costs, property taxes, utilities, equipment, insurance, and benefits). These include all the expenses you pay outside of labor costs — things like building costs, property taxes, and utilities — and they can be calculated either monthly or annually, depending on the needs of your business. To figure it out, just divide your total annual overhead costs by the number of employees at your business. This will help determine how much an employee costs their employer per hour.
The material price variance calculation tells managers how much money was spent or saved, but it doesn’t tell them why the variance happened. One common reason for unfavorable price variances is a price change from the vendor.
Labor price variance, or rate variance, measures the difference between the budgeted hourly rate and the actual rate you pay direct labor workers who directly manufacture your products. Labor efficiency variance measures the difference between the number of direct labor hours you budgeted and the actual hours your employees work.