How to Calculate Overhead Allocation
A fixed cost remains unchanged even if the related level of activity or volume changes. This step requires adding indirect materials, indirect labor, and all other product costs not included in direct materials and direct labor. Here, overhead is estimated to include indirect materials ($50 worth of coffee), indirect labor ($150 worth of maintenance), and other product costs ($200 worth of rent), for a total of $400. In the scenario with the soda bottler above, the facility lease payments are still owed even if no current production takes place within the facility. Likewise, the company still incurs other business expenses, such as insurance payments and administrative and management salaries.
What is included in factory overhead?
Factory overhead is the costs incurred during the manufacturing process, not including the costs of direct labor and direct materials. Factory overhead is normally aggregated into cost pools and allocated to units produced during the period.
Fixed costs, on the other hand, are all costs that are not inventoriable costs. All costs that do not fluctuate directly with production volume are fixed costs. Fixed costs include various indirect costs and fixed manufacturing overhead costs. Variable costs include direct labor, direct materials, and variable overhead. These can include rent or mortgage payments, depreciation of assets, salaries and payroll, membership and subscription dues, legal fees and accounting costs.
Manufacturing overhead, however, consists of indirect factory-related costs and as such must be divided up and allocated to each unit produced. For example, the property tax on a factory building is part of manufacturing overhead. Although the property tax covers an entire year and appears as one large amount on just one tax bill, GAAP requires that a portion of this amount be allocated or assigned to each product manufactured during that year. Manufacturing overhead (also referred to as factory overhead, factory burden, and manufacturing support costs) refers to indirect factory-related costs that are incurred when a product is manufactured.
Overheads are also very important cost element along with direct materials and direct labor. In accounting, all costs can be described as either fixed costs or variable costs. Variable costs are inventoriable costs – they are allocated to units of production and recorded in inventory accounts, such as cost of goods sold.
However, when business is slow, the best place to cut expenses is in the overhead activities because cutting production activities has a direct detrimental effect on revenue production. Direct costs can be conveniently traced down to the product manufactured. On the other hand, indirect costs cannot be identified with the product manufactured.
Factory overhead
Overhead expenses are other costs not related to labor, direct materials, or production. They represent more static costs and pertain to general business functions, such as paying accounting personnel and facility costs. A manufacturer’s product costs are the direct materials, direct labor, and manufacturing overhead used in making its products.
Examples of product costs are direct materials, direct labor, and allocated factory overhead. Examples of period costs are general and administrative expenses, such as rent, office depreciation, office supplies, and utilities. Office rent, insurance, office furniture, company cars, professional memberships and other expenses that do not change from year to year are called fixed overhead. The mortgage payment or rent of the factory building is a fixed overhead expense.
Overhead expenses are all costs on the income statement except for direct labor, direct materials, and direct expenses. Overhead expenses include accounting fees, advertising, insurance, interest, legal fees, labor burden, rent, repairs, supplies, taxes, telephone bills, travel expenditures, and utilities.
Join PRO or PRO Plus and Get Lifetime Access to Our Premium Materials
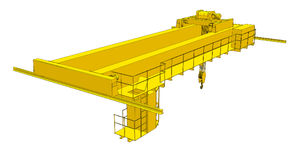
The period costs are reported as expenses in the accounting period in which they 1) best match with revenues, 2) when they expire, or 3) in the current accounting period. In addition to the selling and general administrative expenses, most interest expense is a period expense. Manufacturing overheads are all costs endured by a business that is within the physical platform in which the product or service is created. Difference between manufacturing overheads and administrative overheads is that manufacturing overheads are categorized within a factory or office in which the sale takes place.
Costs incurred off the production floor include utilities, insurance expenses and property taxes for the manufacturing facility. For a product to be profitable, its selling price must be greater than the sum of the product cost (direct material, direct labor, and manufacturing overhead) plus the nonmanufacturing costs and expenses. Manufacturing overhead includes such things as the electricity used to operate the factory equipment, depreciation on the factory equipment and building, factory supplies and factory personnel (other than direct labor). How these costs are assigned to products has an impact on the measurement of an individual product’s profitability. A company can cut back on the purchase of office supplies, generally without harming the production of goods and services that produce revenue.
- Direct materials are those materials (including purchased parts) that are used to make a product and can be directly associated with the product.
In a business, all costs not directly related to the production and sale of products and services that create revenues for the business are called overhead costs. Overhead may be fixed or variable in cost just as the costs associated with production and sale of the company’s products can be either fixed or variable. Suppose a simple factory makes two products — call them Product A and Product B. The factory needs no direct materials (yes, that means it makes products out of thin air; please suspend your disbelief).
In the production department of a manufacturing company, depreciation expense is considered an indirect cost, since it is included in factory overhead and then allocated to the units manufactured during a reporting period. The treatment of depreciation as an indirect cost is the most common treatment within a business. Period costs are not a necessary part of the manufacturing process. As a result, period costs cannot be assigned to the products or to the cost of inventory. The period costs are usually associated with the selling function of the business or its general administration.
Fixed expense amounts stay the same regardless if a business earns more — or loses more — in revenue that month. Associated payroll costs, including outsourcing payroll services, are included in the fixed expense category. Labor costs, such as employee time, that are not chargeable to a direct manufacturing or production activity also fall under fixed expenses.
Manufacturing overhead consists of the expenses incurred in your manufacturing process less your direct material and labor costs. Some production floor costs are the wages paid to forklift drivers, material handlers, product inspectors, quality-control inspectors, and equipment repair and maintenance personnel.
The costs of selling the product are operating expenses (period cost) and not part of manufacturing overhead costs because they are not incurred to make a product. Overhead also includes all costs involved in manufacturing with the exception of the cost of raw materials. In business, overhead or overhead expense refers to an ongoing expense of operating a business. Overheads are the expenditure which cannot be conveniently traced to or identified with any particular cost unit, unlike operating expenses such as raw material and labor. Therefore, overheads cannot be immediately associated with the products or services being offered, thus do not directly generate profits.
Whilst administrative overheads is typically categorized within some sort of back-office or supporting office. Although there are cases when the two physical buildings may overlap, it is the usage of the overheads that separates them. This includes office equipment such as printer, fax machine, computers, refrigerator, etc. They are equipment that do not directly result in sales and profits as they are only used for supporting functions that they can provide to business operations. However, equipment can vary between administrative overheads and manufacturing overheads based on the purpose of which they are using the equipment.
Overhead relates more to the administrative functions of an enterprise such as accounting, human resources, clerical and managerial staff, supplies and equipment. Overhead is the organizational structure that houses the revenue-producing activities.
For example, for a printing company a printer would be considered a manufacturing overhead. Note that all of the items in the list above pertain to the manufacturing function of the business. Rather, nonmanufacturing expenses are reported separately (as SG&A and interest expense) on the income statement during the accounting period in which they are incurred. As their names indicate, direct material and direct labor costs are directly traceable to the products being manufactured.
Manufacturing Overhead (Explanation)
Any cost other than the direct cost of labor and the direct cost of materials is considered a form of overhead. Factory overhead — also commonly referred to as manufacturing overhead — is used to describe some indirect costs associated with manufacturing products.
Materials directly used to make a product — called direct materials — are not considered factory overhead. For example, wood pulp is a direct material needed for the manufacture of paper. However, the oil used to keep the equipment running smoothly is an example of an indirect material used in the manufacture of paper. Like indirect labor costs, the cost of indirect materials used in manufacturing is considered a form of factory overhead. Overhead refers to certain costs a business incurs when producing a product.
However, overheads are still vital to business operations as they provide critical support for the business to carry out profit making activities. For example, overhead costs such as the rent for a factory allows workers to manufacture products which can then be sold for a profit.
Depreciation on factory equipment, factory rent, factory insurance, factory property taxes, and factory utilities are all examples of manufacturing overhead costs. Together, the direct materials, direct labor, and manufacturing overhead are referred to as manufacturing costs.
Direct materials are those materials (including purchased parts) that are used to make a product and can be directly associated with the product. Some materials used in making a product have a minimal cost, such as screws, nails, and glue, or do not become part of the final product, such as lubricants for machines and tape used when painting. Such materials are called indirect materials and are accounted for as manufacturing overhead. Manufacturing overhead costs include indirect materials, indirect labor, and all other manufacturing costs.