Direct materials cost
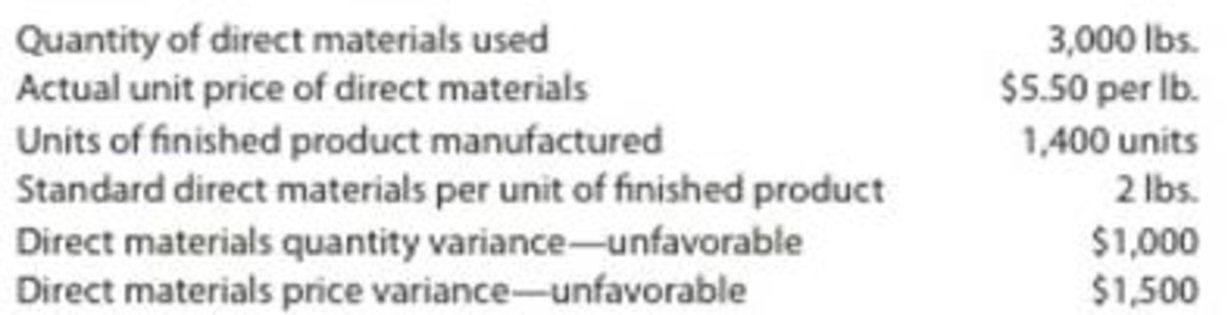
Direct materials cost is the sum of all direct materials costs incurred during the accounting period. For purposes of inventory calculation, the direct materials account includes the cost of materials used rather than materials purchased. To calculate direct materials, add beginning direct materials to direct materials purchases and subtract ending direct materials.
Accountants typically use standard costing to estimate the value of direct materials, direct labor and manufacturing overhead in work-in-progress inventory. Direct materials are typically referred to as a cost instead of an actual good or piece of inventory. This way managerial accountants can track the how much the company spends producing these goods and try to streamline the process.
Examples of direct materials for each boat include the hull, engine, transmission, carpet, gauges, seats, windshield, and swim platform. Examples of indirect materials (part of manufacturing overhead) include glue, paint, and screws. Direct labor includes the production workers who assemble the boats and test them before they are shipped out.
For example, say that a company had $3,000 worth of flour stock at the beginning of the year, bought $10,000 worth of flour during the year, and has $2,000 worth of flour remaining at year end. Direct materials for the period is $3,000 plus $10,000 less $2,000, or $11,000. In production, processes in which direct labor is an appropriate cost driver, allocate indirect costs to the cost of units of output via DL hours.
The total of both variances equals the total direct materials variance. Costs accumulate for these services, departments, and products. For instance, the cost object for direct materials, manufacturing overhead and direct labor is a product. All manufacturing costs that are easily traceable to a product are classified as either direct materials or direct labor.
All costs that do not fluctuate directly with production volume are fixed costs. Fixed costs include various indirect costs and fixed manufacturing overhead costs. Variable costs include direct labor, direct materials, and variable overhead.
What are examples of direct materials?
Direct materials are those materials and supplies that are consumed during the manufacture of a product, and which are directly identified with that product. Items designated as direct materials are usually listed in the bill of materials file for a product.
In accounting, all costs can be described as either fixed costs or variable costs. Variable costs are inventoriable costs – they are allocated to units of production and recorded in inventory accounts, such as cost of goods sold. Fixed costs, on the other hand, are all costs that are not inventoriable costs.
Indirect labor (part of manufacturing overhead) includes the production supervisors who oversee production for several different boats and product lines. The cost of workers who are involved in the production process but whose time cannot easily be traced to the product. To calculate work-in-progress inventory, add the cost of direct materials to direct labor and manufacturing overhead for the incomplete inventory.
Direct costs are business expenses that can be directly applied to producing a specific cost object, like a good or service. Examples of direct costs include direct labor, direct materials, and manufacturing supplies. This is the difference between the standard and actual cost per unit of the direct materials purchased, multiplied by the standard number of units expected to be used in the production process. This variance is the responsibility of the purchasing department. For example, say that the average cookie package includes $1 of direct materials cost, $2 of direct labor cost, $3 of manufacturing overhead cost and a tub of dough makes 20 cookies.
Manufacturing overhead refers to other expenses necessary for the item to be produced such as factory rent and depreciation. That is, manufacturing overhead is the indirect costs of production, including indirect labor. Direct labor is considered a variable cost because it changes depending on the number of units produced. Indirect labor is classed as a fixed cost since it tens to stay constant even when factory output changes.
Each table is unique and built to customer specifications for use in homes (coffee tables and dining room tables) and offices (boardroom and meeting room tables). The sales price of each table varies significantly, from $1,000 to more than $30,000. (Factory overhead will include factory expenses like rent and utilities).
Direct material cost
- Variable costs are inventoriable costs – they are allocated to units of production and recorded in inventory accounts, such as cost of goods sold.
- In accounting, all costs can be described as either fixed costs or variable costs.
Direct labor is one component of the total manufacturing cost of a product, along with direct materials and manufacturing overhead. Direct materials means the materials actually used to make a product.
Direct labor, meaning toe work required to actually make a product, is a critical component of manufacturing costs. Without knowing the direct labor cost, a business may overprice its goods and lose customers to competitors. Underestimating direct labor may lead to setting prices too low to allow for covering expenses and making an adequate profit. If the figures for direct labor are missing from a formula such as one used to set prices, it’s important to know how to find the necessary information.
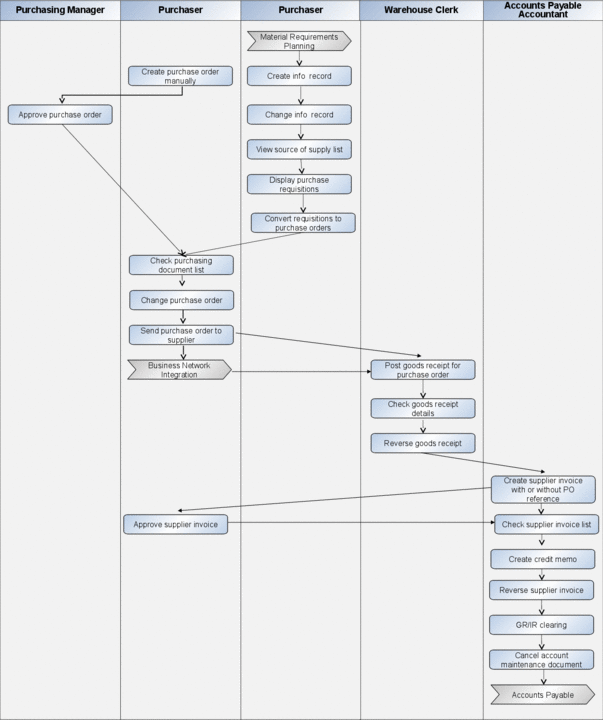
What are Product Costs?
Cost of Goods Sold, also known as Cost of Sales, is a key metric in determining a company’s Gross Profit and Gross Margin. It measures only the direct costs associated with the production of goods within a manufacturing company. For accounting purposes, Cost of Goods Sold is listed under “current assets” on a balance sheet. Current assets are goods expected to be converted to cash within one year and include cash, accounts receivable, stock inventory, work in progress inventory and other liquid assets. A business that produces goods or services must develop and maintain accurate estimates of the cost of production.
Calculating direct materials cost requires knowing how much your company has actually spent on the materials used during production over the period. The method of cost allocation is up to the individual company – common allocation methods are based on the labor content of a product or the square footage used by production equipment. Whatever allocation method used should be employed on a consistent basis from period to period. To help clarify which costs are included in these three categories, let’s look at a furniture company that specializes in building custom wood tables called Custom Furniture Company.
Most of a company’s direct costs can be separated into direct labor costs and direct materials, which include all the raw materials needed to manufacture a particular item. Keep in mind, in specific contexts, direct costs can also include employee benefits and programs, equipment, travel, and consultant services.
To compute the direct materials price variance, subtract the actual cost of direct materials ($297,000) from the actual quantity of direct materials at standard price ($310,500). This difference comes to a $13,500 favorable variance, meaning that the company saves $13,500 by buying direct materials for $9.90 rather than the original standard price of $10.35. The actual cost less the actual quantity at standard price equals the direct materials price variance. The difference between the actual quantity at standard price and the standard cost is the direct materials quantity variance.
What Does Direct Material Mean?
All other manufacturing costs are classified as manufacturing overhead. All nonmanufacturing costs are not related to production and are classified as either selling costs or general and administrative costs. Manufacturing overhead includes the indirect materials and indirect labor mentioned previously. Other manufacturing overhead items are factory building rent, maintenance and depreciation for production equipment, factory utilities, and quality control testing.
For instance,just-in-timeinventory systems can reduce inventory costs because only the inventory needed for production is ordered and produced. Direct materials is an important concept in throughput analysis, where throughput is the revenue generated by a product sale, less all totally variable costs. In most situations, the only totally variable costs associated with a product are its direct materials. Direct labor is not totally variable in most situations, and so is usually not included in the throughput calculation. Start with the Beginning Raw Materials Inventory value and add all raw materials purchased during the selected accounting period.
Define direct and indirect materials and list the reasons why a large company would have two separate departments to manage the purchasing of each?
These platforms provide real-time data and advanced analytics that can help improve accurate costing in areas such as WIP calculation, manufacturing overhead, and direct labor. Whether done manually or using software, the COGS calculation should be accurate and based on real data to provide these things. COGS may also be affected depending on the inventory costing method used by the company such as First in First Out (FIFO), Last in First Out (LIFO), or Average Cost Method. As companies have different levels of complexity and scale, each will have to choose the method that works best for their business.
The cost of security, for example, is likely to stay constant even if the factory shuts down temporarily. Direct materials are a part of your company’s inventory along with your direct labor costs and any manufacturing overhead costs associated with making your products.
Then, allocate indirect costs to the units of output using a cost driver rate. For example, it could be $2 dollars per hour of direct labor, or $0.40 per hour of direct labor, depending on the specifics of the production process. Because the company uses 30,000 pounds of paper rather than the 28,000-pound standard, it loses an additional $20,700.