Departments to manage the purchasing
Product Costs
Direct materials are a part of your company’s inventory along with your direct labor costs and any manufacturing overhead costs associated with making your products. Calculating direct materials cost requires knowing how much your company has actually spent on the materials used during production over the period. Having this information allows you to analyze your inventory costs and determine your work-in-progress inventory, which is inventory that is not completely finished at the time you do your analysis. To help clarify which costs are included in these three categories, let’s look at a furniture company that specializes in building custom wood tables called Custom Furniture Company. Each table is unique and built to customer specifications for use in homes (coffee tables and dining room tables) and offices (boardroom and meeting room tables).
Product Costs Template
For instance,just-in-timeinventory systems can reduce inventory costs because only the inventory needed for production is ordered and produced. Direct materials are those that are used directly in the production process and are reflected in the final product. For example, timber would be a direct material in the production of furniture.
Identify whether each item listed in item 2 should be categorized as direct materials, direct labor, manufacturing overhead, selling cost, or general and administrative cost. The following manufacturing items are for a construction company working on several custom homes. Identify whether each item should be categorized as direct materials, direct labor, or manufacturing overhead. Organizing business expenses as either direct costs or indirect costs is a matter that goes beyond simple product pricing – it affects your tax payments, too. Overhead expenses, such as the utilities that power equipment and the inventory needed to manage the office, are tax-deductible.
Free Accounting Courses
This includes items such as software, equipment and raw materials. It can also include labor, assuming the labor is specific to the product, department or project. Direct materials are typically referred to as a cost instead of an actual good or piece of inventory. This way managerial accountants can track the how much the company spends producing these goods and try to streamline the process.
Understanding the Costs in Product Costs
Examples of indirect costs are production supervision salaries, quality control costs, insurance, and depreciation. Product costs are costs that are incurred to create a product that is intended for sale to customers. Product costs include direct material (DM), direct labor (DL), and manufacturing overhead (MOH). Direct costs are business expenses that can be directly applied to producing a specific cost object, like a good or service.
Direct materials cost is the sum of all direct materials costs incurred during the accounting period. For purposes of inventory calculation, the direct materials account includes the cost of materials used rather than materials purchased.
Direct materials for the period is $3,000 plus $10,000 less $2,000, or $11,000. Examples of direct costs are direct labor, direct materials, commissions, piece rate wages, and manufacturing supplies.
Direct labor is considered a variable cost because it changes depending on the number of units produced. Indirect labor is classed as a fixed cost since it tens to stay constant even when factory output changes. The cost of security, for example, is likely to stay constant even if the factory shuts down temporarily. Manufacturing overhead includes the indirect materials and indirect labor mentioned previously. Other manufacturing overhead items are factory building rent, maintenance and depreciation for production equipment, factory utilities, and quality control testing.
Accountants typically use standard costing to estimate the value of direct materials, direct labor and manufacturing overhead in work-in-progress inventory. The cost of workers who are involved in the production process but whose time cannot easily be traced to the product. In the case of the company A ltd, all the expenses mentioned will be included in the direct material costs except the cost incurred for paying the wages to the employees.
- Direct materials are a part of your company’s inventory along with your direct labor costs and any manufacturing overhead costs associated with making your products.
Examples of direct costs include direct labor, direct materials, and manufacturing supplies. Indirect materials are those that are used in the production of the final product indirectly. They cannot be directly measured and conveniently charged to the cost of production. For example, in furniture production, wood, glue, and nails may be classified as indirect materials. To calculate work-in-progress inventory, add the cost of direct materials to direct labor and manufacturing overhead for the incomplete inventory.
What is direct material cost example?
Direct material cost. Direct material cost is the cost of the raw materials and components used to create a product. The materials must be easily identifiable with the resulting product (otherwise they are considered to be joint costs).
What is direct and indirect material?
Labor and direct materials, which are used in creating a specific product, constitute the majority of direct costs. For example, to create its product, an appliance maker requires steel, electronic components and other raw materials. Two popular ways of tracking these costs, determining whether and when your company actually uses materials in production, include last in, first out (LIFO) or first in, first out (FIFO). This can be helpful when the costs of materials fluctuate in the course of production.
In some cases, even the costs of goods sold qualify for deductions; they reflect expenses incurred from selling products. It can be tempting to misclassify direct costs as indirect, but this can get you in a lot of trouble if you’re audited by the IRS. Direct costs are expenses that a company can easily connect to a specific “cost object,” which may be a product, department or project.
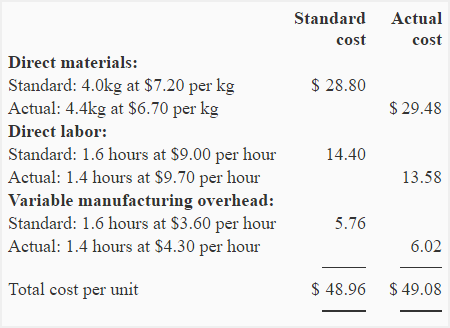
Examples of direct materials for each boat include the hull, engine, transmission, carpet, gauges, seats, windshield, and swim platform. Examples of indirect materials (part of manufacturing overhead) include glue, paint, and screws. Direct labor includes the production workers who assemble the boats and test them before they are shipped out. Indirect labor (part of manufacturing overhead) includes the production supervisors who oversee production for several different boats and product lines.
The sales price of each table varies significantly, from $1,000 to more than $30,000. Direct labor is one component of the total manufacturing cost of a product, along with direct materials and manufacturing overhead.
How do you calculate direct material cost?
Direct material costs are the costs of raw materials or parts that go directly into producing products. For example, if Company A is a toy manufacturer, an example of a direct material cost would be the plastic used to make the toys.
To calculate direct materials, add beginning direct materials to direct materials purchases and subtract ending direct materials. For example, say that a company had $3,000 worth of flour stock at the beginning of the year, bought $10,000 worth of flour during the year, and has $2,000 worth of flour remaining at year end.
For example, say that the average cookie package includes $1 of direct materials cost, $2 of direct labor cost, $3 of manufacturing overhead cost and a tub of dough makes 20 cookies. If one pound of dough is left at the end of the accounting period, the work-in progress value is $6 (the sum of direct materials, direct labor and overhead costs) multiplied by 20 cookies, or $120. All manufacturing costs that are easily traceable to a product are classified as either direct materials or direct labor. All other manufacturing costs are classified as manufacturing overhead. All nonmanufacturing costs are not related to production and are classified as either selling costs or general and administrative costs.
Direct materials means the materials actually used to make a product. Manufacturing overhead refers to other expenses necessary for the item to be produced such as factory rent and depreciation. That is, manufacturing overhead is the indirect costs of production, including indirect labor.