Cost of poor quality
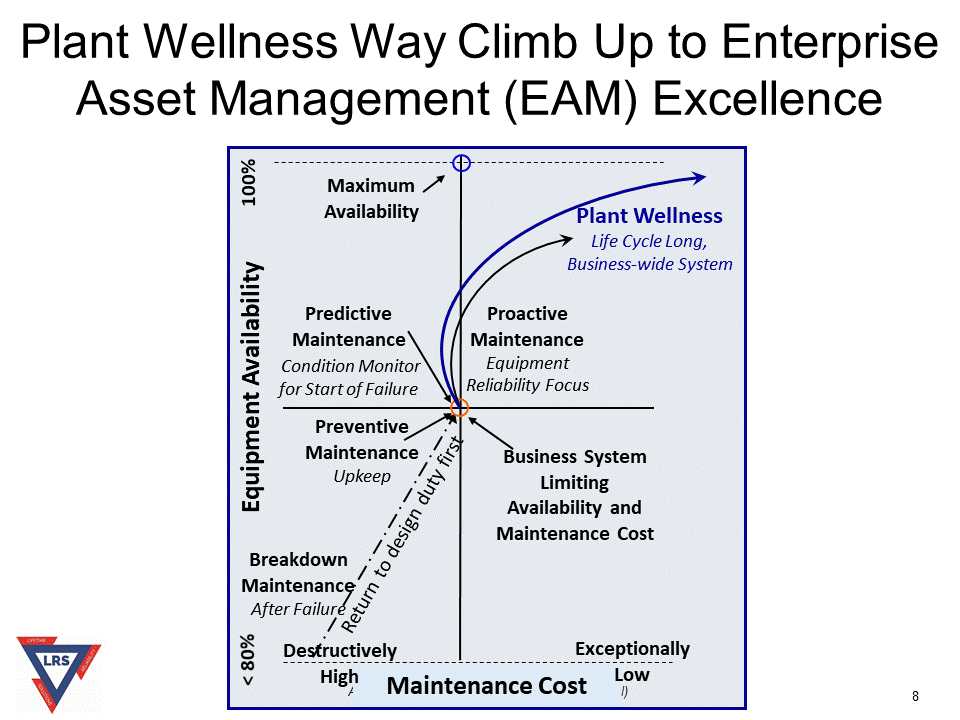
Similarly, the time and people resources a company devotes to handling customer complaints reflects a cost of poor quality. External failure costs are incurred during customer use and can include defective products, warranty charges, customer complaints, replacement products, recalls and repairs. While external costs are the most apparent, these costs sometimes can be difficult to quantify. Therefore, businesses fail to include them in the overall quality costs because failures such as poor packaging and handling issues are not always reported by the customer.
Examples of internal failure cost
Within the total amount of quality cost, however, COPQ represents only a certain proportion. Costs do not result from only producing and fixing failures; a high amount of costs comes from ensuring that good products are produced.
Accounting for Management
Inspection cannot build quality into a product, but will sort out some of the junk. If junk is not produced in the first place, there is no need to pay for the junk and for the inspection. In the example above, the Cost of Poor Quality (CoPQ) was having a major impact on the bottom line.
They inspect fabrics for defects, garment measurements for fitting, print for registration and correct colour, stock from receiving to shipping and think they are doing good, efficient, quality control. In fact, in some businesses 100% inspection is considered the best level of quality control available. One should ask why inspecting a product after the operation is completed (i.e. after making the mistake).
Examples of prevention cost
The project resulted in a positive impact on the bottom line of $140,000 in the first year. Alpha Company has since implemented processes to measure and reduce scrap, improved process controls and introduced new quality metrics throughout the organization. They are now actively measuring and evaluating both the cost of good quality and poor quality. Preventive costs are any expenditures incurred that are intended to minimize the number of defects in products and services. For example, a company could invest in training programs for the operators of its production machinery, to ensure that they understand how to manufacture parts correctly.
Prevention costs:
They are the costs to rectify the defects, correspondence with the manufacturer for complaint settlement, business loss due to poor quality received and expenses to repair the loss of reputation. This part of the section focuses on the question “How much is it costing our organization by not doing a good job on quality? Now, the prevention costs, which normally should be a bit high to offset the failure costs, are seen at a low of about 1.2%.
- The external field failure costs are incurred by the manufacturer because the customer is supplied with an unacceptable product or service.
- Besides the direct costs of poor quality incurred by the manufacturer, customers also incur costs, which are termed as indirect external field failure costs.
- It is the cost incurred by the company because the appraisal system did not detect all the errors before the product or service was delivered.
The external field failure costs are incurred by the manufacturer because the customer is supplied with an unacceptable product or service. It is the cost incurred by the company because the appraisal system did not detect all the errors before the product or service was delivered. Besides the direct costs of poor quality incurred by the manufacturer, customers also incur costs, which are termed as indirect external field failure costs.
Through an investment in the Cost of Good Quality (CoGQ), Alpha Company achieved a significant reduction in the Cost of Quality. There are opportunities for improvement in processes at most organizations. It has been estimated that the Cost of Quality usually amounts to between 15-40% of business costs.
More focus is needed on part of the company to install preventive mechanisms so that the failure costs are reduced. Total Cost of Quality is the aggregate cost of poor quality or product failures- including scrap, rework, and warranty costs- as well as expenses incurred to prevent or resolve quality problems(including the cost of inspection). In calculations for Best Plants entries, do not include costs of normal maintenance, quality training, or quality-related equipment upgrades. The appraisal costs are mainly related to the monitoring and measuring of the activities related to the quality of the services and products. When calculating the business case for a Six Sigma project, the cost of poor quality (COPQ), which is the cost caused through producing defects, is a commonly used concept.
Alpha Company once measured Cost of Quality as the amount of warranty cost versus total sales. It was discovered that customer part shortages originating from one work cell were resulting in warranty costs of over $400,000 in one year. A team was formed to investigate and perform Root Cause Analysis (RCA) of the shortages and a plan was developed to redesign the work cell for an estimated cost of $60,000. With management approval, the work cell was redesigned with a revised layout, pick bins, dedicated locations for all the parts, process controls were defined and implemented and several additional improvements were made.
They just segregate bad products from good, but do not prevent the errors. When most people think about quality control, they normally think about people inspecting a product i.e. quality control inspectors.
This article explains the cost of quality as a more comprehensive concept covering the cost of poor quality and the cost of good quality. In short, any cost that would not have been expended if quality were perfect contributes to the cost of quality. The field failure costs are results of failures either before are after the materials are dispatched.
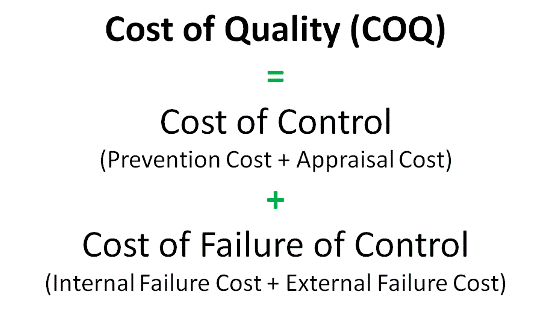
The failures before despatch are internal field failures which also include the cost incurred in rectifying an error before the product or service is accepted by the customer. To accurately account for the of quality costs on a small business’ budget, it is imperative to understand the hidden quality costs such as loss of sales and customer service. Many businesses include warranties in their quality costs, but they often underestimate the full financial impact if the product fails after the warranty expires. Even though the customer incurs the cost of replacing the failed product, the experience may discourage the customer from purchasing from that company again, resulting in loss of sales.
What is prevention cost example?
Preventive costs are any expenditures incurred that are intended to minimize the number of defects in products and services. Preventive costs are considered part of the cost of quality.
The goal of implementing Cost of Quality methodology is to maximize product quality while minimizing cost. Cost of Quality methodology provides the detailed information that management needs to accurately evaluate the effectiveness of their quality systems, identify problem areas and opportunities for improvement.
Comments on Costs of quality or quality costs
The changes reduced tact times and the number of operators required for the process. This provided resources for the addition of quality technicians to regularly audit and maintain the process on all shifts. Within the first year of operation, shortages were reduced by 50% equaling a $200,000 reduction in warranty costs.