Cost of Goods Sold Journal Entry
How to Take a Reserve Against Your Inventory
On the other hand, failure to properly inventory a supply chain with necessary MRO items can result in production shut-downs and slow-downs, diminished product availability, and ultimately customer attrition. Inventory items at any of the three production stages can change in value. Changes in value can occur for a number of reasons including depreciation, deterioration, obsolescence, change in customer taste, increased demand, decreased market supply, and so on. An accurate inventory accounting system will keep track of these changes to inventory goods at all three production stages and adjust company asset values and the costs associated with the inventory accordingly. As such, the purpose of each seems to be that of maintaining a high level of customer service or part of an attempt to minimize overall costs.
Buffer inventory is the inventory kept or purchased for the purpose of meeting future uncertainties. Also known as safety stock, it is the amount of inventory besides the current inventory requirement. The benefit is smooth business flow and customer satisfaction and disadvantage is the carrying cost of inventory. Raw material as buffer stock is kept for achieving nonstop production and finished goods for delivering any size, any type of order by the customer. Oftentimes, firms will purchase and hold inventory that is in excess of their current need in anticipation of a possible future event.
What is the double entry for inventory?
Create a journal entry When adding a COGS journal entry, you will debit your COGS Expense account and credit your Purchases and Inventory accounts. Purchases are decreased by credits and inventory is increased by credits. You will credit your Purchases account to record the amount spent on the materials.
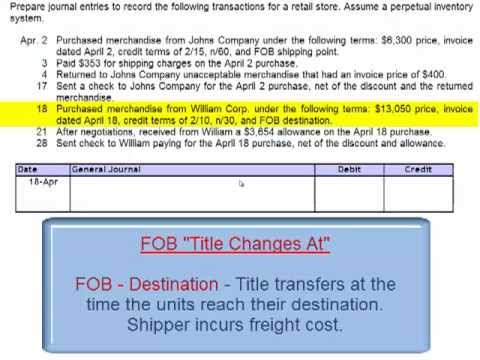
Such events may include a price increase, a seasonal increase in demand, or even an impending labor strike. Therefore, the firm has avoided both excessive overtime due to increased demand and hiring costs due to increased demand. It also has avoided layoff costs associated with production cut-backs, or worse, the idling or shutting down of facilities.
Typically, raw materials are commodities such as ore, grain, minerals, petroleum, chemicals, paper, wood, paint, steel, and food items. However, items such as nuts and bolts, ball bearings, key stock, casters, seats, wheels, and even engines may be regarded as raw materials if they are purchased from outside the firm. Debit the work-in-process inventory account and credit the raw materials inventory asset account. Or, if the production process is brief, bypass the work-in-process account and debit the finished goods inventory account instead.
Double entry accounting
If the firm is a manufacturer, it must maintain some inventory of raw materials and work-in-process in order to keep the factory running. In addition, it must maintain some supply of finished goods in order to meet demand. Under periodic inventory procedure, companies do not use the Merchandise Inventory account to record each purchase and sale of merchandise. Instead, a company corrects the balance in the Merchandise Inventory account as the result of a physical inventory count at the end of the accounting period. Also, the company usually does not maintain other records showing the exact number of units that should be on hand.
How do you record inventory in general journal?
Transaction Upon Selling
You credit the finished goods inventory, and debit cost of goods sold. This action transfers the goods from inventory to expenses. When you sell the $100 product for cash, you would record a bookkeeping entry for a cash transaction and credit the sales revenue account for the sale.
Economic order quantity (EOQ) is the ideal order quantity a company should purchase to minimize inventory costs such as holding costs, shortage costs, and order costs. This production-scheduling model was developed in 1913 by Ford W. Harris and has been refined over time. The formula assumes that demand, ordering, and holding costs all remain constant. These are the partly processed raw materials lying on the production floor. It is unavoidable inventory which will be created in almost any manufacturing business.
Raw materials are inventory items that are used in the manufacturer’s conversion process to produce components, subassemblies, or finished products. These inventory items may be commodities or extracted materials that the firm or its subsidiary has produced or extracted. They also may be objects or elements that the firm has purchased from outside the organization. Even if the item is partially assembled or is considered a finished good to the supplier, the purchaser may classify it as a raw material if his or her firm had no input into its production.
Inventory is a quantity of goods owned and stored by a business that is intended either for resale or as raw materials and components used in producing goods that the business sells. For example, motherboards warehoused at a computer company to be used in the assembling of its computer systems are inventory. The products displayed for sale and stored in the backrooms of a department store are inventory as well.
- Inventory is either the finished goods stored and offered for sale by a business or the raw materials used by a company to produce finished products.
- Three general types of inventory control systems include continuous review systems, periodic review systems, and just-in-time inventory control.
- An inventory control system is a process businesses use to manage inventory.
Raw materials may be aggregated into a single inventory line item in the balance sheet that also includes the cost of work-in-process and finished goods inventory. In accounting, the inventory turnover is a measure of the number of times inventory is sold or used in a time period such as a year. This ratio tests whether a company is generating a sufficient volume of business based on its inventory.
The equation forinventory turnover is the cost of goods sold (COGS) divided by the average inventory. Inventory turnover is also known as inventory turns, stockturn, stock turns, turns, and stock turnover.
How to Record a Cost of Goods Sold Journal Entry
If you are operating a production facility, then the warehouse staff will pick raw materials from stock and shift it to the production floor, possibly by job number. This calls for another journal entry to officially shift the goods into the work-in-process account, which is shown below. If the production process is short, it may be easier to shift the cost of raw materials straight into the finished goods account, rather than the work-in-process account. The calculation also assumes that both ordering and holding costs remain constant. When inventory falls to a certain level, the EOQ formula, if applied to business processes, triggers the need to place an order for more units.
Debit the factory overhead account and credit the raw materials inventory asset account. At the end of the month, the ending balance in the overhead account is allocated to the cost of goods sold and ending inventory. Raw materials inventory is the total cost of all component parts currently in stock that have not yet been used in work-in-process or finished goods production.
Bookkeeping Entries for Inventory Transactions
By determining a reorder point, the business avoids running out of inventory and can continue to fill customer orders. If the company runs out of inventory, there is a shortage cost, which is the revenue lost because the company has insufficient inventory to fill an order. An inventory shortage may also mean the company loses the customer or the client will order less in the future. The goal of the EOQ formula is to identify the optimal number of product units to order. If achieved, a company can minimize its costs for buying, delivery, and storing units.
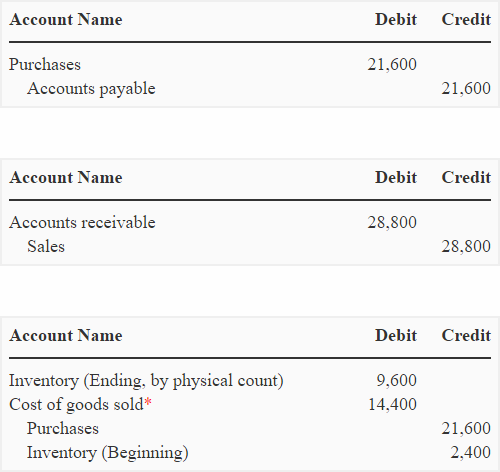
This process is sometimes called “smoothing” because it smoothes the peaks and valleys in demand, allowing the firm to maintain a constant level of output and a stable workforce. These goods are maintained on hand at or near a business’s location so that the firm may meet demand and fulfill its reason for existence. If the firm is a retail establishment, a customer may look elsewhere to have his or her needs satisfied if the firm does not have the required item in stock when the customer arrives.
Thus, they mistakenly assume items that have been stolen have been sold and include their cost in cost of goods sold. Raw materials of all types are initially recorded into an inventory asset account with a debit to the raw materials inventory account and a credit to the accounts payable account. The cost of raw materials on hand as of the balance sheet date appears in the balance sheet as a current asset.
Three general types of inventory control systems include continuous review systems, periodic review systems, and just-in-time inventory control. Raw materials may sometimes be declared obsolete, possibly because they are no longer used in company products, or because they have degraded while in storage, and so can no longer be used. If so, they are typically charged directly to the cost of goods sold, with an offsetting credit to the raw materials inventory account. Consolidating MRO suppliers, when possible, also makes good fiscal sense, as shaving even just a few percentage points from an MRO budget can radically improve a company’s bottom line.
Inventory is either the finished goods stored and offered for sale by a business or the raw materials used by a company to produce finished products. An inventory control system is a process businesses use to manage inventory.
If you buy $100 in raw materials to manufacture your product, you would debit your raw materials inventory and credit your accounts payable. Once that $100 of raw material is moved to the work-in-process phase, the work-in-process inventory account is debited and the raw material inventory account is credited.
Although periodic inventory procedure reduces record-keeping, it also reduces control over inventory items. Firms assume any items not included in the physical count of inventory at the end of the period have been sold.