Comparison of Job Costing with Process Costing
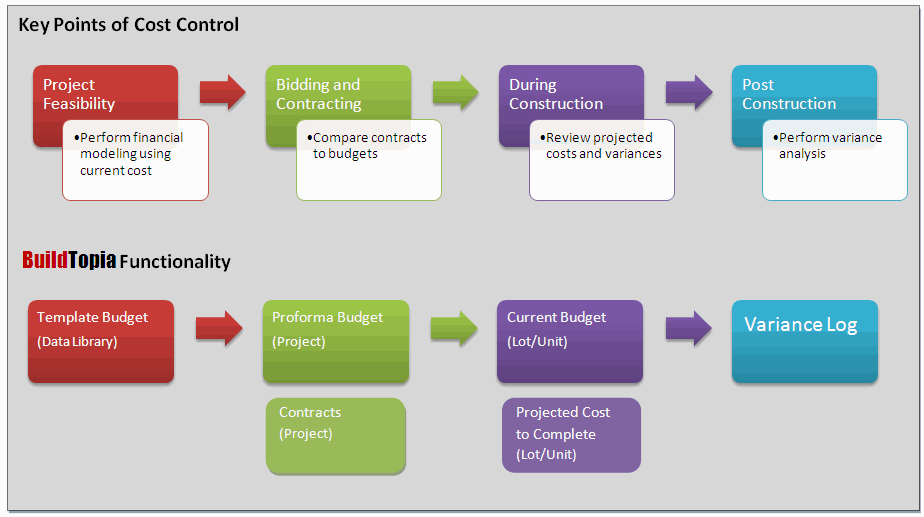
Inventory Accounts Similarities Inventory accounts include raw materials inventory, work-in-process inventory, and finished goods inventory. Differences Process Costing Job Costing Several different work-in-process inventory accounts are used—one for each department (or process). One work-in-process inventory account is used—job cost sheets track costs assigned to each job. Job Costing is the process of determining the labor and materials cost for each job in a systematic way, and then using this information to create a quote for the customer.
Job costing, also called project-based accounting, is the process of tracking costs and revenue for each individual project. Job costing looks at each project in detail, breaking down the costs of labor, materials and overhead. Business concerns which undertake the production of components or parts in batches adopt batch costing. Under this system, the cost of each batch is ascertained separately.
What companies use job order costing and process costing?
The difference between job costing and process costing. Job costing involves the detailed accumulation of production costs attributable to specific units or groups of units. Process costing involves the accumulation of costs for lengthy production runs involving products that are indistinguishable from each other.
Product Costs Similarities Product costs consist of direct materials, direct labor, and manufacturing overhead. Differences Process Costing Job Costing Product costs are assigned to departments (or processes). Unit Cost Information Similarities Unit cost information is needed by management for decision-making purposes. Differences Process Costing Job Costing Unit cost information comes from the departmental production cost report.
1 Comparison of Job Costing with Process Costing
ABC is generally used as a tool for understanding product and customer cost and profitability based on the production or performing processes. As such, ABC has predominantly been used to support strategic decisions such as pricing, outsourcing, identification and measurement of process improvement initiatives.
All other methods are combinations, extensions or improvements of these basic methods. Process costing is a type of operation costing which is used to ascertain the cost of a product at each process or stage of manufacture. CIMA defines process costing as “The costing method applicable where goods or services result from a sequence of continuous or repetitive operations or processes. Costs are averaged over the units produced during the period”.
In either case, once overhead/burden is added, the total cost for the job can be determined. Of course, in the days of computerized job costing software, journaling costs manually is an obsolete process. Such hand-journaling is mandatory for companies that continue to use general accounting software to do job costing. Enlightened accountants are moving forward and using job costing software, thereby improving cost control, reducing risk, and increasing the chance of profitability.
Process costing is suitable for industries producing homogeneous products and where production is a continuous flow. A process can be referred to as the sub-unit of an organization specifically defined for cost collection purpose.
Job costing or cost accounting can be used in virtually any industry (especially service industry) to ensure that the product pricing covers actual costs, overhead and provides a profit. The purpose of any business is to make money, and job costing is the most effective way to ensure that occurs. In a job costing system, costs may be accumulated either by job or by batch. For a typical job, direct material, labor, subcontract costs, equipment, and other direct costs are tracked at their actual values. Overhead or “burden” may be applied either by using a rate based on direct labor hours or by using some other Activity Based Costing cost driver.
However, job costing does not work for manufacturing companies that produce products that are identical, or very similar, such as food or oil, because each unit costs the same to produce. Process costing systems allocate expenses to products by adding total costs at each stage of the manufacturing process then dividing these costs by the total number of units produced. This enables these companies to determine the costs associated with the products at each stage of the manufacturing process and cut costs as necessary per stage of manufacture.
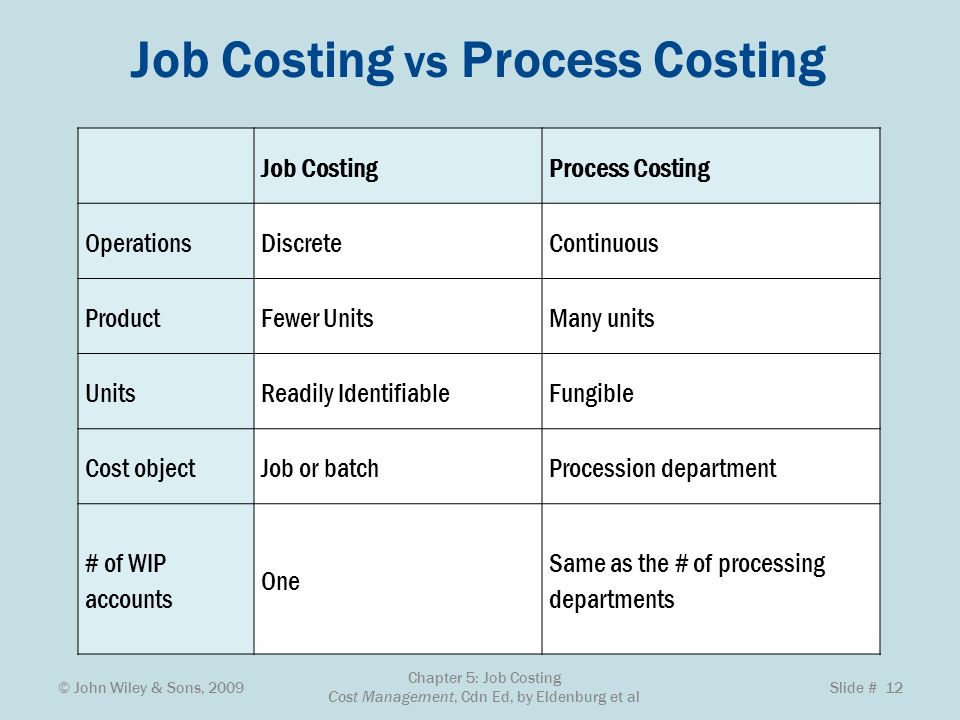
- Unit Cost Information Similarities Unit cost information is needed by management for decision-making purposes.
- Product Costs Similarities Product costs consist of direct materials, direct labor, and manufacturing overhead.
As distinct from job costing, in these industries the cost of each process is determined for a given period of time. Products lose their individual identity as they are manufactured in a continuous flow.
Recall the three components of product costs—direct materials, direct labor, and manufacturing overhead. Assigning these product costs to individual products remains an important goal for process costing, just as with job costing. However, instead of assigning product costs to individual jobs (shown on a job cost sheet), process costing assigns these costs to departments (shown on a departmental production cost report). Costing is an accounting technique used to determine the exact expenses for materials, labor and overhead incurred in operations. Job order costing records the actual materials and labor expenses for specific jobs, and assigns overhead to jobs at a pre-determined rate.
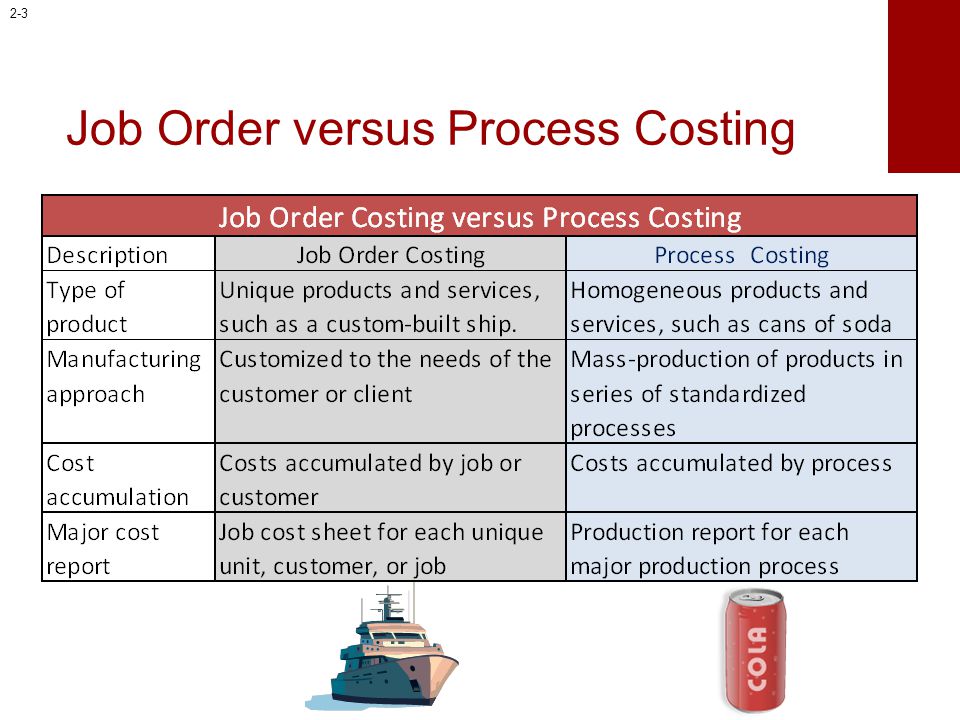
Full Costing Method
Process costing applies costs to departments based on the average number of units produced per day. Job order and process costing have unique advantages and disadvantages that make them best suited for specific situations. Direct materials are materials that are consumed during the manufacture of a product. To determine the cost per unit under process costing, each expense must first be assigned to a process then categorized as a direct materials cost or conversion cost. Once these steps have been completed, the expenses can be divided by total units produced to obtain the cost per unit.
(Batch means of group of similar products/ identical products). The cost per unit of each batch is ascertained by dividing the cost of each batch by the number of units produced in that batch. Shoe factories, Drug factories, Biscuit factories, readymade garments toy manufacturing concerns etc. adopt this method. In industries where a continuous process of production is carried and the product is homogeneous, the method of ascertaining the cost of the product is called Process Costing.
Robin Cooper and Robert S. Kaplan, proponents of the Balanced Scorecard, brought notice to these concepts in a number of articles published in Harvard Business Review beginning in 1988. Cooper and Kaplan described ABC as an approach to solve the problems of traditional cost management systems. These traditional costing systems are often unable to determine accurately the actual costs of production and of the costs of related services. Consequently, managers were making decisions based on inaccurate data especially where there are multiple products. In a business organization, the ABC methodology assigns an organization’s resource costs through activities to the products and services provided to its customers.
Absorption vs Variable Costing Meaning
Job costing and process costing are the two basic methods of costing. Job costing is suitable to industries which manufacture or execute the work according to the specifications of the customers. Process costing is suitable to industries where production is continuous and the units produced are identical.