Activity-Based Costing in Healthcare Saves Millions
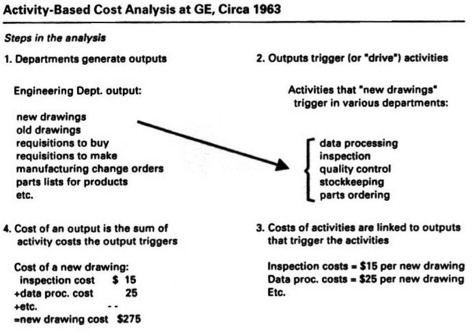
Activity-based costing is an improved method for allocating overhead costs. Instead of using one factor for cost allocation, this new method focuses on different aspects of the production process and allocates the overhead based on each product’s reliance on different overhead aspects. The first stage of allocation determines the cost of each occurrence of an overhead event during the process.
It increases understanding of overheads and cost drivers; and makes costly and non-value adding activities more visible, allowing managers to reduce or eliminate them. ABC enables effective challenge of operating costs to find better ways of allocating and eliminating overheads. It also enables improved product and customer profitability analysis.
The accounting costs incurred to maintain such a system can be prohibitively high. The split of cost helps to identify cost drivers, if achieved. Direct labour and materials are relatively easy to trace directly to products, but it is more difficult to directly allocate indirect costs to products. Where products use common resources differently, some sort of weighting is needed in the cost allocation process. The cost driver is a factor that creates or drives the cost of the activity.
How is absorption costing treated under GAAP?
The second stage allocates the cost of each occurrence to individual items produced by the business. We have discussed three different methods of allocating overhead to products—plantwide allocation, department allocation, and activity-based costing. Remember, total overhead costs will not change in the short run, but the way total overhead costs are allocated to products will change depending on the method used. If SailRite produces 2,000 units of the Deluxe boat, will the unit cost remain at $5,030?
The companies that used activity-based costing (ABC) had higher overhead costs as a percent of total product costs than companies that used traditional costing. The complexity of production processes and products tended to be higher for those using ABC, and ABC companies operated at capacity more frequently. The ABC column represents overhead costs allocated using the activity-based costing shown back in Figure 3.5 “Allocation of Overhead Costs to Products at SailRite Company”. Activity-based costing (ABC) is a methodology for more precisely allocating overhead costs by assigning them to activities.
Once costs are assigned to activities, the costs can be assigned to the cost objects that use those activities. The system can be employed for the targeted reduction of overhead costs.
The following estimates are for the activities and related cost drivers identified as having the greatest impact on overhead costs. This is the same cost figure used for the plantwide and department allocation methods we discussed earlier. Activity-based costing simply provides a more refined way to allocate the same overhead costs to products. Activity cost pools are groups of individual costs that are influenced by the same cost drivers, which are activities that control the amount of costs incurred.
This is done by dividing the estimated overhead costs (from step 2) by the estimated level of cost driver activity (from step 3). Figure 3.4 “Predetermined Overhead Rates for SailRite Company” provides the overhead rate calculations for SailRite Company based on the information shown in the previous three steps. These levels include batch-level activity, unit-level activity, customer-level activity, organization-sustaining activity, and product-level activity. Activity-based costing provides a more accurate method of product/service costing, leading to more accurate pricing decisions.
Treating fixed costs as variable
They are an important part of activity-based costing, because they allow companies to group similar overhead costs together, which enables the companies to allocate overhead based on multiple criteria. Overhead cost is an indirect cost, providing common benefit to the production of different lines of products or rendering of a range of services. Unlike direct labor and material costs that can be traced to specific products or services as direct contributing resources, overhead cost is a shared resource that may not be easily traced back to a particular product or service.
- Activity cost pools are an important part of activity-based costing as they enable companies to group similar overhead costs together and divide by a common cost driver.
- This enables the companies to have multiple criteria for allocating overhead instead of just one like in traditional costing systems.
- Activity-based costing allows for more accurate product costing than other types of costing method because it requires the calculation of multiple rates to allocate manufacturing overhead to products.
What is cost accounting?
Activity-based costing allows for more accurate product costing than other types of costing method because it requires the calculation of multiple rates to allocate manufacturing overhead to products. Activity cost pools are an important part of activity-based costing as they enable companies to group similar overhead costs together and divide by a common cost driver.
What is Activity Based Costing with example?
Activity-based costing (ABC) is a costing method that identifies activities in an organization and assigns the cost of each activity to all products and services according to the actual consumption by each. This model assigns more indirect costs (overhead) into direct costs compared to conventional costing.
The total overhead expense would be divided by the total number of direct labor hours for the financial period. Using the per-hour overhead rate, overhead cost would be applied to each item based on the number of direct labor hours used in producing the good.
Manufacturing companies use product costing techniques to determine how much it costs to manufacture each product it produces. Activity-based costing systems allocate manufacturing overhead by assigning indirect costs to activity cost pools, then dividing each cost pool by a cost driver to obtain the rates used for allocation. Manufacturing overhead costs are the expenses incurred in the manufacture of a product that cannot be directly allocated to that product. Activity cost pools are groups of individual costs influenced by the same cost drivers , which are activities that control the amount of costs incurred. The management of Parker Company would like to use activity-based costing to allocate overhead rather than use one plantwide rate based on direct labor hours.
A significant portion of overhead costs are fixed and will be spread out over more units, thereby reducing the cost per unit. The point here is that managers must beware of using per unit cost information blindly for decision making, particularly if a significant change in the level of production is anticipated. Assigning costs to activities takes time, as does identifying and tracking cost drivers. And assigning costs to products requires a significant amount of time in the accounting department. Imagine having 15 cost pools (activities), each with a predetermined overhead rate used to assign overhead costs to the company’s 80 products—not an unrealistic example for a large company.
Activity-Based Costing (ABC)
For the year, there were 2,500 labor hours worked, which in this example is the cost driver. Calculating the cost driver rate is done by dividing the $50,000 a year electric bill by the 2,500 hours, yielding a cost driver rate of $20. Activity-based costing (ABC) is a costing method that assigns overhead and indirect costs to related products and services. This accounting method of costing recognizes the relationship between costs, overhead activities, and manufactured products, assigning indirect costs to products less arbitrarily than traditional costing methods. However, some indirect costs, such as management and office staff salaries, are difficult to assign to a product.
This enables the companies to have multiple criteria for allocating overhead instead of just one like in traditional costing systems. Activity-based costing is the newest means of calculating how overhead expenses are allocated to different products at the time of publication. The traditional allocation method requires the business to pick one metric to use as a means to allot overhead costs.
Methodology
It supports performance management techniques such as continuous improvement and scorecards. A survey of 130 U.S. manufacturing companies yielded some interesting results.
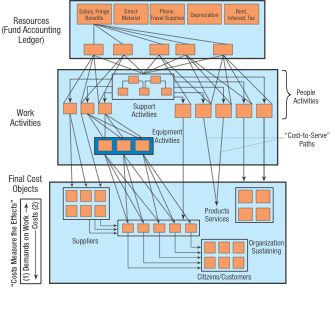
Generally, the business would try to select a metric that is the underlying cause of overhead costs. For example, a business might choose direct labor hours as the allocation metric.
ABC works best in complex environments, where there are many machines and products, and tangled processes that are not easy to sort out. Conversely, it is of less use in a streamlined environment where production processes are abbreviated. As an activity-based costing example, consider Company ABC that has a $50,000 per year electricity bill. The number of labor hours has a direct impact on the electric bill.